Localised silver plating for bus bar
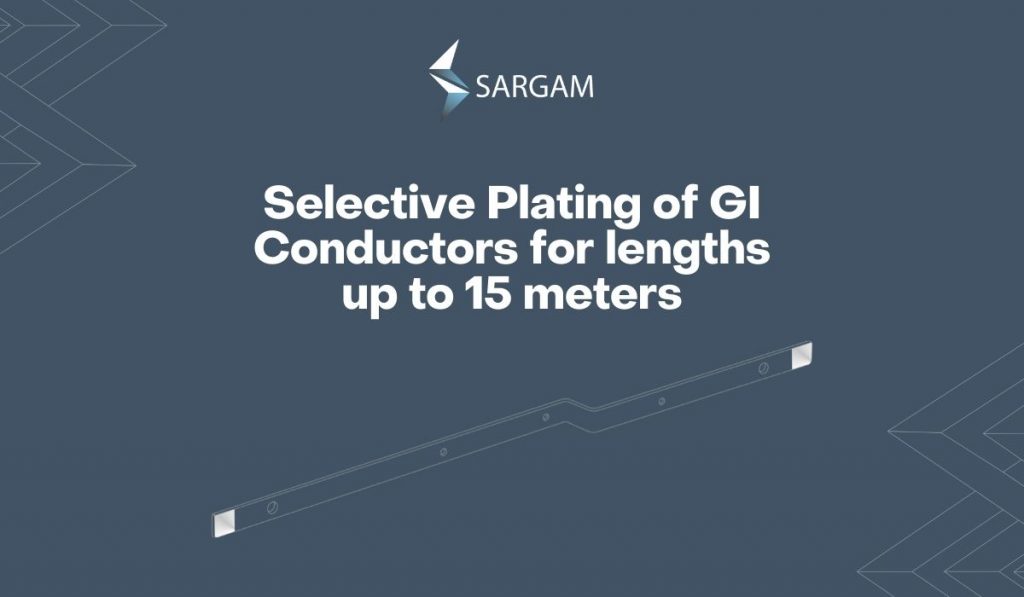
The generation, transmission, and distribution of power require an optimized power flow. Such optimization can be achieved best by enabling low resistance conductive joints with silver plating. This shows especially better results in the case of bus bars. Studies have shown that silver-plated bus bars provide more stable contact resistance than unplanted ones. Stable contact resistance joints also mean a reduced risk of failures, lower need for frequent maintenance, and a drastic reduction in downtime. Lastly, the plated bus bars work at a lower operating temperature, increasing the service life of the contact joints.
IEEE standards as well as key government regulations mandate that the bolted bus connections should be plated in line with application specifications.
An effective bus bar coating should apply a uniform and sufficiently thick deposit to provide corrosion resistance and increase the surface area of the bus joint by providing a levelling effect.
The in-place plating of the bus systems can be done in the most cost-effective manner with brush plating. Brush plating enables the bus systems to be plated during routine maintenance. This way, when a capacity increase in the overall system is required, the bus systems can simply be upgraded rather than replaced with new bus bars.
What are the issues with unplated bus bars?
With the increasing demand for power, the pressure to perform is growing on bus bars. Constraints of the economy and market forces are now leading the manufacturers to find economical ways to improve the efficiency and performance of bus bars.
Key threats that limit the performance and lifespan of bus bars include
Oxidation
A barrier coating is necessary to prevent the oxidation of the bus material. Oxidation layers are formed within the joints of the bus material leading to increased resistance. This in turn fuels an increase in local temperature and in voltage drops. Reports suggest that oxidation can increase the joint resistance in uncoated bus bars by as much as 20%. Silver plating the joints can significantly reduce the instances of oxidation when the bus bars are in operation.
Irregularities in mating surfaces
Even in new bus bars, only around 10% of the copper surface could come in direct contact with the connection owing to the imperfect copper surface. The high areas could be flattened by increasing the contact force, but this could place undue stress on the fastening system while limiting the intended effects to a minimum.
Contamination of the material with particulates before installation.
Even in the case of bolted contacts, contaminants from the ambient atmosphere can create a non-conductive surface film, affecting the reliability of joints. The contact resistance of thin surface films can be reduced by fritting, but thicker films may still remain. These remaining films still pose a threat. What’s worse, increased resistance leads to a rise in temperature at the joint, which magnifies the threat posed by films.
Fritting occurs when a contact film witnesses a dielectric breakdown. This breakdown could be caused by even a potential gradient of 100V/μm
These threats reduce the efficiency and lifespan of bus bar joints over time. Together, they increase the contact resistance and temperature which can form hot spots and lead to system failure.
How can silver plating help?
Field test and practical application experience demonstrate that plating the joints with around 0.0002” to 0.0005” thick deposits of tin, nickel, or silver can improve the performance of the joints by as much as 30% while significantly reducing the need for maintenance.
A plating of soft material such as silver creates a compressive gasket on the surfaces to be connected. When the surfaces are bolted together with sufficient force, the conductive material is squeezed into the lower areas reducing the joints’ resistance and increasing the contact area.
The silver plating slows down the formation of surface films and copper oxide, reducing the heat and enabling better conductivity. It also allows the joint to operate at a higher temperature without degradation over the joint’s lifespan
Why silver
Silver’s softness enables the metal to adhere more precisely to the contours and crevices of the original piece, increasing the actual contact area. Apart from being a good electrical conductor itself, silver inhibits the formation of copper oxide at the mating faces. Nickel is often used in plating joints to save on costs, but silver exhibits less resistance than nickel plating, keeps the temperatures lower, and delivers better operating performance and efficiency.
Achieving uniform and sufficient plating thickness for bus bars is a challenge. To get around this issue, a complete bus bar is subjected to a tank plating the connection in a cyanide silver bath. This process entails high costs and incurs downtime as bus bars are removed and sent offsite for plating.
Sargam Industries enables silver plating of bus bars to be done on-site without taking the part in question away from the location. We use digital ampere-hour meters to exercise tight control over plating thickness and deliver smooth, uniform plating. To ensure the total safety of the operator and the personnel at your facility, Sargam uses a non-cyanide silver solution.
Considering the application requirements, the required plating thickness for each part is precisely calculated before the commencement of the plating.
Saving replacement costs with in-place silver plating
With changing electrical regulations, bus duct systems might need to be replaced with newer and higher-rated systems. However, many instances in the West, such as the TVA regulations have shown that older bus system can cater to higher ratings when empowered with in-place silver plating. Precise brush plating can increase the current-carrying capacity as well as efficiency of the system at much lower costs.
For successful results of in-place silver plating, the modified bolted joints of the bus system should be stable and operate at a reduced contact resistance for a wider operating rate.
To sum up, silver plating enables compliance of older bus bars with higher ratings at much less cost than replacement.